Charging the Industry with Great Service and Fast Delivery!!
An industry trailblazer for almost 50 years, our goal is to provide you, our valued customer, with exceptional service, quality material and fast delivery.
As a leading supplier of precision flat ground stock, drill rod, and tool steel off-cuts, we deliver top-tier solutions tailored to your industry’s needs. Explore our commitment to quality and precision today.
Order online to get started!
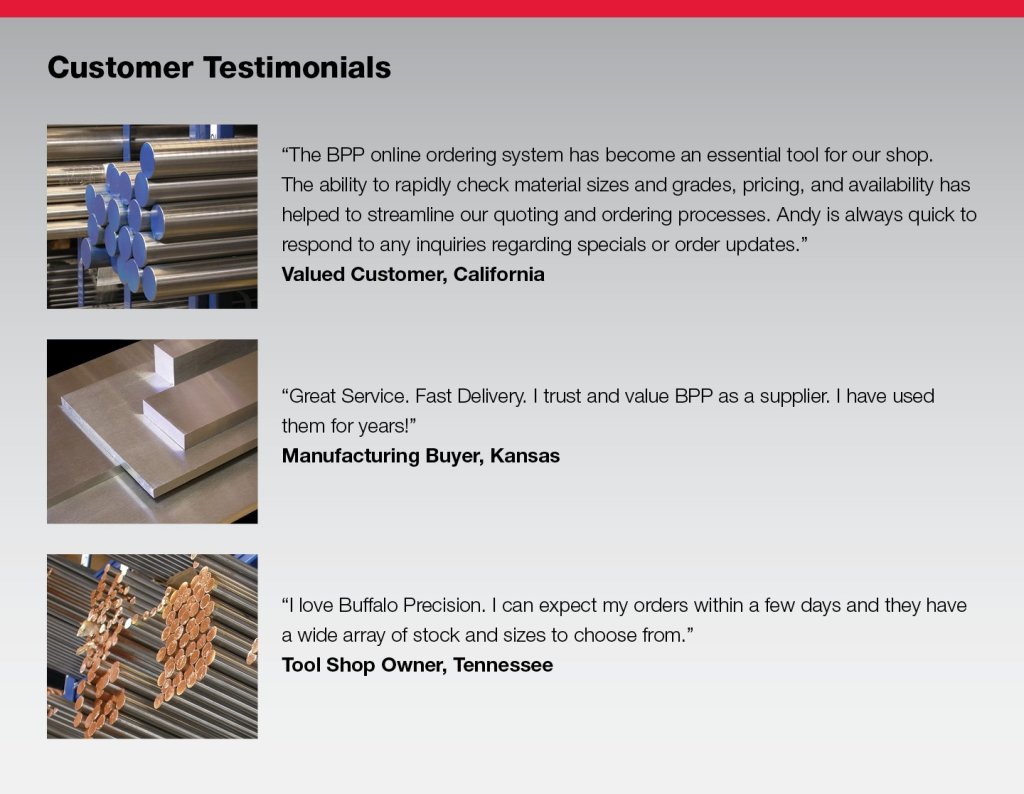
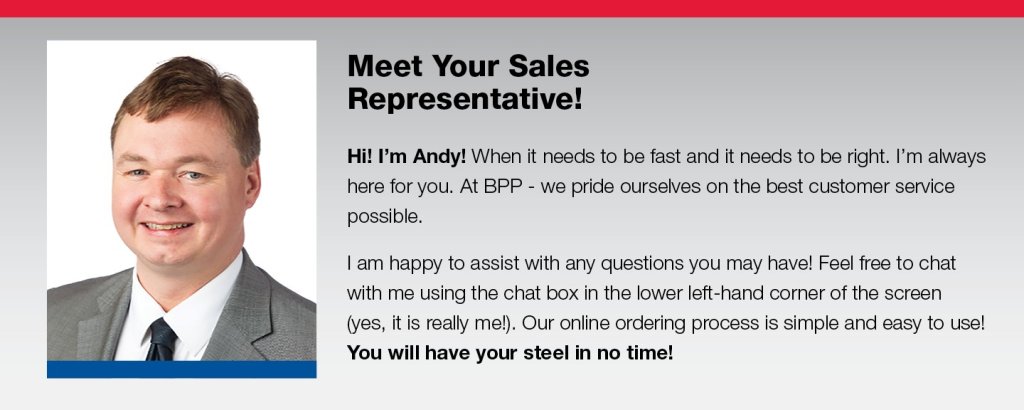